How does it work?
In the pump’s volute, fluid enters the pump axially through the eye of the impeller (low-pressure area), which rotates at high speed. As the impeller and blades rotate, they transfer momentum to incoming fluid. The fluid accelerates radially outward from the pump chasing, and a vacuum is created at the impeller’s eye that continuously draws more fluid into the pump. As the fluid’s velocity increases, its kinetic energy increases. The fluid of high kinetic energy is forced out of the impeller area and enters the volute. The fluid flows through a continuously increasing cross-sectional area in the volute, where the kinetic energy is converted into fluid pressure (according to Bernoulli’s principle).
The impeller blades are usually backward-curved, but there are also radial and forward-curved blade designs. The output pressure slightly changes according to the design used. The blades may be open or closed. Also, the diffuser may be fitted with fixed vanes to help guide the flow toward the exit. The energy transferred to the liquid corresponds to the velocity at the edge of the impeller. The faster the impeller revolves or, the bigger the impeller is, the higher will the velocity head be.
Main Parts of a Centrifugal Pump
Each centrifugal pump is made of hundreds of parts. There are a few components that virtually every centrifugal pump has in common. These components can be subdivided into the wet end and the mechanical end.
The wet end of the pump includes those parts that determine the hydraulic performance of the pump. The two primary wet ends are the impeller and casing. In some cases, the first radial bearing can be water lubricated. In this case, also bearing can belong to wet ends.
The mechanical end includes those parts that support the impeller within the casing. The mechanical end of the pump includes the pump shaft, sealing, bearings, and shaft sleeve.
These components are designed to perform specific tasks:
Impeller. The impeller is a rotor used to increase the kinetic energy of the flow.
- Casing (Volute). The casing contains the liquid and acts as a pressure containment vessel that directs the liquid flow through the centrifugal pump. The volute is a curved funnel that increases in area as it approaches the discharge port. The volute of a centrifugal pump is the casing that receives the fluid being pumped by the impeller, slowing down the fluid’s flow rate. Therefore, according to Bernoulli’s principle, the volute converts kinetic energy into pressure by reducing speed while increasing pressure. Some centrifugal pumps contain diffusers. A diffuser is a set of stationary vanes that surround the impeller. The diffuser directs the flow, allows a more gradual expansion, and therefore increases the efficiency of the centrifugal pump.
- Shaft (Rotor). The impeller is mounted on a shaft. A shaft is a mechanical component for transmitting torque from the motor to the impeller.
- Shaft sealing. Centrifugal pumps are provided with packing rings or mechanical seal, which helps prevent the leakage of the pumped liquid.
- Bearings. Bearings constrain the relative motion of the shaft (rotor) and reduce friction between the rotating shaft and the stator. There are at least 5 common types of bearing, each of which operates on different principles:
- Plain bearing
- Rolling-element bearing
- Jewel bearing
- Fluid bearing
- Magnetic bearing
Types of Impellers in Centrifugal Pumps
Impeller design is the most significant factor for determining the performance of a centrifugal pump. A properly designed impeller optimizes flow while minimizing turbulence and maximizing efficiency.
The impeller of a centrifugal pump can be of three basic types:
- Open impeller. Open impellers have the vanes free on both sides. Open impellers are structurally weak. They are typically used in small-diameter, inexpensive pumps and pumps handling suspended solids.
- Semi-open impeller. The vanes are free on one side and enclosed on the other. The shroud adds mechanical strength. They also offer higher efficiencies than open impellers. They can be used in medium-diameter pumps and with liquids containing small amounts of suspended solids. Because of the minimization of recirculation and other losses, it is very important that a small clearance exists between the impeller vanes and the casing.
- Closed impeller. The vanes are located between the two discs, all in a single casting. They are used in large pumps with high efficiencies and low required Net Positive Suction Head. The centrifugal pumps with closed impellers are the most widely used pumps handling clear liquids. They rely on close-clearance wear rings on the impeller and the pump casing. The closed impeller is a more complicated and expensive design because of the impeller, but additional wear rings are needed.
The impeller blades can be:
- Backward-curved blade design (preferred design due to the negative slope of performance curve)
- Radial blade design
- Forward-curved blade design (due to positive slope conditions, this design can cause pump surge)
Impellers can be either:
- Single-suction. A single-suction impeller allows liquid to enter the center of the blades from only one direction.
- Double-suction. A double-suction impeller allows liquid to enter the center of the impeller blades from both sides simultaneously. This reduces forces exerted on the shaft.
The output pressure slightly changes according to the design used. The blades may be open or closed. Also, the diffuser may be fitted with fixed vanes to help guide the flow toward the exit. The energy transferred to the liquid corresponds to the velocity at the edge of the impeller. The faster the impeller revolves or, the bigger the impeller is, the higher will the velocity head be.
In general, centrifugal pumps can be classified based on how fluid flows through the pump. It is not classification based on the impeller alone but based on the design of the pump casing and the impeller. The three types of flow through a centrifugal pump are:
- radial flow
- mixed-flow (part radial, part axial)
- axial flow (propeller type)
Performance Characteristics of Centrifugal Pumps
Although the theory of centrifugal pumps gives many qualitative results, the most important indicator of a pump’s performance lies in extensive hydraulic testing.
In industry, the characteristics of all pumps are usually read from their Q-H curve or performance curve (flow rate – height). As can be seen, the performance charts use a discharge – Q (usually in m3/h) and pump head – H (usually in m) as basic performance variables.
System Head
In the chapter on head loss, it was determined that both major losses and minor losses in piping systems are proportional to the square of the flow velocity. The system head loss must be directly proportional to the square of the volumetric flow rate because the volumetric flow rate is directly proportional to the flow velocity.
It must be added that the open hydraulic systems contain not only the friction head but also the elevation head, which must be considered. The elevation head (static head) represents the potential energy of a fluid due to its elevation above a reference level.
In many cases, the total head of a system is a combination of elevation head and friction head, as shown in the figure.
Most of the hydraulic systems are closed hydraulic loops in nuclear engineering, and these systems only have friction head (no static head).
Pump Head – Performance Curve
In fluid dynamics, the term pump head is used to measure the kinetic energy which a pump creates. Head is a measurement of the height of the incompressible fluid column the pump could create from the kinetic energy that the pump gives to the liquid. The head and flow rate determine the performance of a pump, which is graphically shown in the figure as the performance curve or pump characteristic curve. The main reason for using head instead of pressure to determine the performance of a centrifugal pump is that the height of the fluid column is not dependent on the specific gravity (weight) of the liquid. In contrast, the pressure from a pump will change. In terms of pressure, the pump head (ΔPpump) is the difference between system backpressure and the pump’s inlet pressure.
The maximum pump head of a centrifugal pump is mainly determined by the outside diameter of the pump’s impeller and the shaft angular velocity – speed of the rotating shaft. The head will also change as the volumetric flow rate through the pump is increased.
When a centrifugal pump is operating at a constant angular velocity, an increase in the system head (back pressure) on the flowing stream causes a reduction in the volumetric flow rate that the centrifugal pump can maintain.
The relationship between the pump head and the volumetric flow rate (Q) that a centrifugal pump can maintain is dependent on various physical characteristics of the pump as:
- the power supplied to the pump
- the angular velocity of the shaft
- the type and diameter of the impeller
and the used fluid:
- fluid density
- fluid viscosity
This relationship is very complicated, and its analysis lies in extensive hydraulic testing of certain centrifugal pumps, as seen in the picture below.
Operating Characteristics of a Hydraulic Loop
When we put together the frictional characteristics (system head) of a hydraulic loop and the performance curve, the result will describe the characteristics of the entire system (e.g.,, one loop of the primary circuit). The following figure shows a typical performance curve for a centrifugal pump related to the frictional system head.
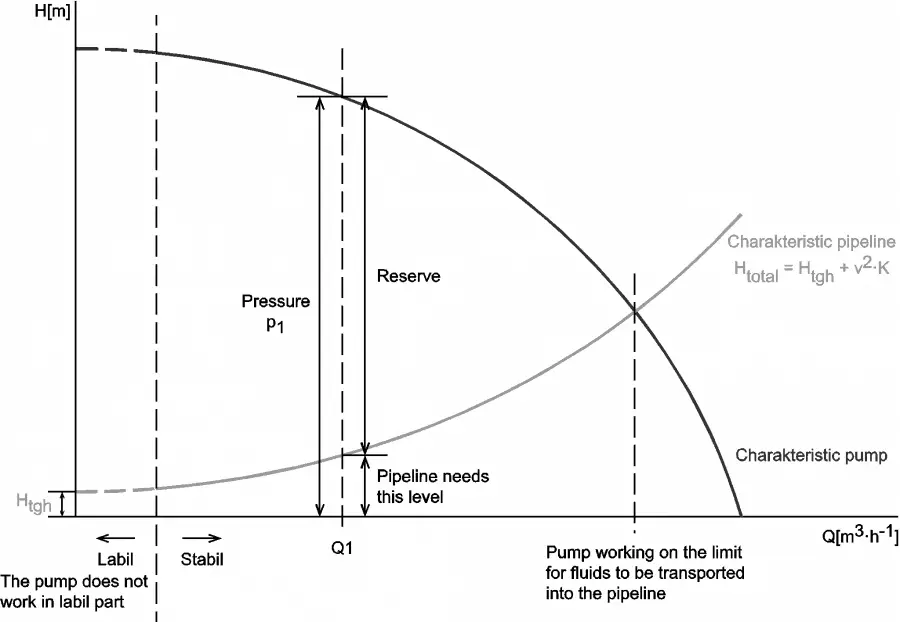
On the vertical axis, the pump head is the difference between system backpressure and the inlet pressure of the pump (ΔPpump). On the horizontal axis, volumetric flow rate (Q ) is the rate at which fluid is flowing through the pump. As can be seen, the head is approximately constant at low discharge and then drops to zero at Qmax. At low discharge, the characteristics can be unstable (with a positive slope of the pump head). These are undesirable characteristics because an unstable pump may start to oscillate between the two possible flow rate combinations, and the pipeline can vibrate.
At flow rate Q1, the pump gains more head than consumes the frictional losses. Therefore the flow rate through the system will increase. The flow rate will stabilize itself at the point where the frictional losses intersect the pump characteristics.
The following terms are defined to characterize the performance of centrifugal pumps:
Series Operation of Centrifugal Pumps (Booster)
Centrifugal pumps are often used in parallel or series to increase the volumetric flow rate or compensate for large major or minor losses.
Series operation of centrifugal pumps is used to overcome large system head loss or gain large pressure increase when liquid is injected into a very high-pressure system (e.g.,, High-Pressure Safety Injection Systems in PWRs, where multi-stage pumps are used).
When a centrifugal pump is operated in a closed-loop, the resulting discharge pressure will be simply the sum of the suction pressure and the pressure normally developed by the pump when operating at zero suction pressure. Therefore it is well suited for use as a booster pump when operated in series. The head produced by two or more pumps is equal to the sum of the individual heads. The volumetric flow rate from the inlet of the first pump to the outlet of the second remains the same. The multi-stage pumps (multiple impeller pumps) are built to reach a higher pump head in practical application.
Parallel Operation of Centrifugal Pumps
Centrifugal pumps are often used in parallel or series to increase the volumetric flow rate in a system or compensate for large major or minor losses.
Parallel operation of centrifugal pumps is used to increase the flow rate through the system. Pumps operating in parallel take their suction from a common header and discharge into a common discharge. While head changes only slightly, flow is almost doubled at any given point. It must be noted the volumetric flow rate is less than twice the flow rate achieved by using a single pump. This is caused by a greater system head loss resulting from a higher flow rate.
Major Failure Modes of Centrifugal Pumps
Since centrifugal pumps are one of the world’s most widely used types of pumps, their operational parameters and vulnerabilities are well known. This article reviews the major failure modes that are found in centrifugal pumps. In general, pump failures result in operational changes that reduce efficiency or may result in a pump breakdown. The reliability of hydraulic systems and also centrifugal pumps are of the highest importance in nuclear engineering.
The failure modes of centrifugal pumps can be grouped into three categories:
Hydraulic Failure Modes
- Cavitation. Cavitation is, in many cases, an undesirable occurrence in centrifugal pumps. Cavitation causes damage to components (erosion of the material), vibrations, noise, and a loss of efficiency.
- Pressure Pulsation. Pressure pulsations are fluctuations in the basic pressure. For high-head pumps, suction and discharge pressure pulsations may cause instability of pump controls, a vibration of suction and discharge piping, and high pump noise levels.
- Pump Recirculation. A pump operating at lower capacity than design limits can suffer from recirculation which occurs internally in the pumps. Pump recirculation can cause surging and cavitation even when the available NPSHa exceeds the supplier’s NPSHr by a considerable margin.
- Radial and Axial Thrust. The high radial thrust resulting in excessive shaft deflections may lead to persistent packing or mechanical seal problems and possibly shaft failure. Axial thrust is imposed along the shaft axis. High axial thrust may impose an excessive load on the bearing.
Mechanical Failure Modes
- Shaft Seizure or Break
- Bearing Failure
- Seal Failure
- Vibrations
- Fatigue
Other Failure Modes
Cavitation in Centrifugal Pumps
Major places where cavitation occurs are in pumps, on impellers, or propellers. In centrifugal pumps, cavitation results from a reduction in suction pressure, an increase in suction temperature, or an increase in the flow rate above the pump has been designed.
There are two basic types of pump cavitation:
Cavitation Number
The Cavitation Number (Ca) or Cavitation Parameter is a dimensionless number used in flow calculations. It is conventional to characterize how close the pressure in the liquid flow is to the vapor pressure (and therefore the potential for cavitation) by means of the cavitation number.
The Cavitation Number can be expressed as:
where
CA = Cavitation Number
p = local pressure (Pa)
pv = vapor pressure of the fluid (Pa)
ρ = density of the fluid (kg/m3)
v = velocity of fluid (m/s)
Cavitation Damage
Cavitation is, in many cases, an undesirable occurrence. In centrifugal pumps, cavitation causes damage to components (erosion of the material), vibrations, noise, and efficiency loss.
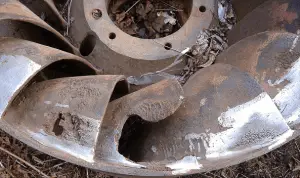
https://commons.wikimedia.org/wiki/File:Turbine_Francis_Worn.JPG
Perhaps the most important engineering problem caused by cavitation is the material damage that cavitation bubbles can cause when they collapse in the vicinity of a solid surface. Cavitation bubbles collapse is a violent process that generates highly localized shock waves and microjets. They force energetic liquid into very small volumes, thereby creating high-temperature spots, and these intense disturbances generate highly localized and transient surface stresses to a solid surface. Signs of erosion will appear as pitting due to the water hammering action of the collapsing vapor bubbles. It has been found that cavitation damage rates increase rapidly with the increase in the volume flow rate.
Softer materials can be damaged even by the short-term occurrence of cavitation. Individual pits can be observed after a single bubble collapse. Therefore harder materials are used for centrifugal pumps. But with the harder materials used in most applications, the cyclic stress due to repeated collapses can cause local surface fatigue failure. Thus cavitation damage to metals usually has the appearance of fatigue failure.
When the cavitation bubbles collapse, they force energetic liquid into very small volumes, thereby creating spots of high temperature and emitting shock waves, the latter of which are a source of the noise. Although the collapse of a small cavity is a relatively low-energy event, highly localized collapses can erode metals, such as steel, over time. The pitting caused by the collapse of cavities produces great to wear on components and can dramatically shorten a propeller or pump’s lifetime.
Cavitation is usually accompanied also by:
- Noise. Collapsing cavities cause typical noise. The level of noise that results from cavitation is a measure of the severity of the cavitation.
- Vibration. Pump vibrations due to cavitation are characteristically low-frequency vibrations, usually found in the 0 to 10 Hz range.
- Reduction in pump efficiency. A decrease in the efficiency of the pump is a more reliable sign of cavitation occurring.