Metal is a material (usually solid) comprising one or more metallic elements (e.g., iron, aluminium, copper, chromium, titanium, gold, nickel), and often also non-metallic elements (e.g., carbon, nitrogen, oxygen) in relatively small amounts. The unique feature of metals, as far as their structure is concerned, is the presence of charge carriers, specifically electrons. The nature of the metallic bond gives this feature. The electrical and thermal conductivities of metals originate from their outer electrons being delocalized.
Metallic Bond
A metallic bond is a chemical bond in which the atoms do not share or exchange electrons to bond together. Instead, many electrons (roughly one for each atom) are more or less free to move throughout the metal so that each electron can interact with many fixed atoms.
The free electrons shield the positively charged ion cores from the mutually repulsive electrostatic forces they would otherwise exert upon one another; consequently, the metallic bond is nondirectional in character. Metallic bonding is found in metals and their alloys. The free movement or delocalization of bonding electrons leads to classical metallic properties such as luster (surface light reflectivity), electrical and thermal conductivity, ductility, and high tensile strength.
Metallurgy
Metallurgy is a domain of materials science and materials engineering that studies the physical and chemical behavior of metallic elements and their alloys.
Metallurgy concerns metals’ chemical, physical, and atomic properties and structures and the principles whereby metals are combined to form alloys. Metallurgy is used to separate metals from their ore.
Metallurgy is subdivided into ferrous metallurgy (the metallurgy of iron and its alloys also known as black metallurgy) and non-ferrous metallurgy (the metallurgy of aluminium, copper, etc.). Ferrous metallurgy involves processes and alloys based on iron, while non-ferrous metallurgy involves processes and alloys based on other metals.
Alloys
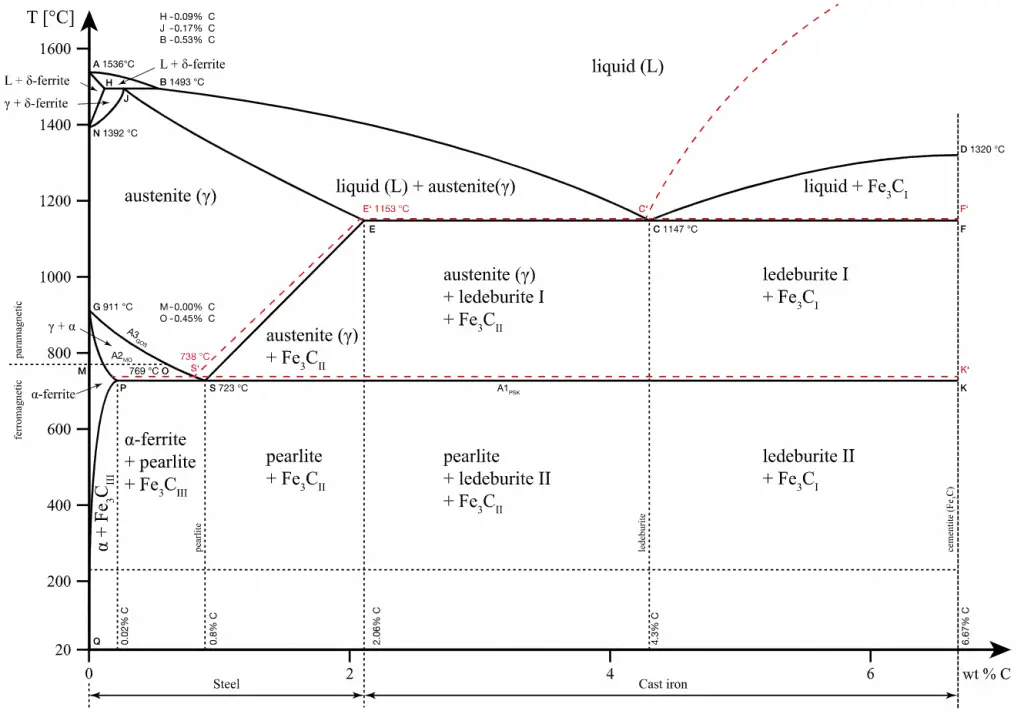
An alloy is a mixture of two or more materials, at least one of which is a metal. Alloys can have a microstructure consisting of solid solutions, where secondary atoms are introduced as substitutionals or interstitials in a crystal lattice. An alloy may also be a mixture of metallic phases (two or more solutions, forming a microstructure of different crystals within the metal). Examples of substitutional alloys include bronze and brass, in which some copper atoms are substituted with either tin or zinc, respectively.
Solid solutions have important commercial and industrial applications, as such mixtures often have superior properties to pure materials. Many metal alloys are solid solutions, and even small amounts of solute can affect the electrical and physical properties of the solvent.
Alloying is a common practice because metallic bonds allow different types of metals to be joined. For example, austenitic stainless steels, including Type 304 stainless steel (containing 18%-20% chromium and 8%-10.5% nickel), have a face-centered cubic structure of iron atoms with the carbon in an interstitial solid solution.
Ferrous alloys, in which iron is the principal constituent, include steel and pig iron (with a carbon content of a few percent) and alloys of iron with other metals (such as stainless steel). Ferrous alloys are known for their strength, and alloys are usually stronger than pure metals, although they generally offer reduced electrical and thermal conductivity. The simplest ferrous alloys are known as steels, and they consist of iron (Fe) alloyed with carbon (C) (about 0.1% to 1%, depending on the type). Adding a small amount of non-metallic carbon to iron trades its great ductility for greater strength. Due to its very-high strength but still substantial toughness, and its ability to be greatly altered by heat treatment, steel is one of the most useful and common ferrous alloys in modern use.
See also: What is a Solid Solution
Processing of Metals
Historically, the processing of metals possesses one of the key domains in materials science. Materials science is one of the oldest forms of engineering and applied science, and the material of choice in a given era is often a defining point (e.g., Stone Age, Bronze Age, Iron Age). Processing metals involves the production of alloys, the shaping, the heat treatment, and the surface treatment of the product. Determining the hardness of the metal using the Rockwell, Vickers, and Brinell hardness scales is a commonly used practice that helps better understand the metal’s elasticity and plasticity for different applications and production processes. Material engineers’ task is to balance material properties such as cost, weight, strength, toughness, hardness, corrosion, fatigue resistance, and performance in temperature extremes. The operating environment must be carefully considered to achieve this goal. In a saltwater environment, ferrous metals and some aluminium alloys corrode quickly. Metals exposed to cold or cryogenic conditions may endure a ductile to brittle transition and lose their toughness, becoming more brittle and prone to cracking. Metals under continual cyclic loading can suffer from metal fatigue. Metals under constant stress at elevated temperatures can creep.
Metalworking Processes
The processing of metals in the solid state can be divided into two major stages:
- Hot working. First, the raw material in the form of large ingots or billets is hot-worked, usually by rolling, forging, or extrusion, into smaller shapes and sizes. These processes occur at a temperature above that at which recrystallization occurs. Being above the recrystallization temperature allows the material to recrystallize during deformation. This is important because recrystallization keeps the materials from strain hardening, ultimately keeping the yield strength and hardness low and ductility high. For hot-working operations, large deformations are possible, which may be successively repeated because the metal remains soft and ductile. In general, metals are shaped by processes such as:
- Forging
- Rolling
- Extrusion
- Drawing
- Casting
- Cold working. Cold working is a metalworking process that occurs below the recrystallization temperature. Because plastic deformation results from the movement of dislocations, metals can be strengthened by preventing this motion. When a metal is plastically deformed, dislocations move, generating additional dislocations. Dislocations can move if the atoms from one of the surrounding planes break their bonds and rebond with the atoms at the terminating edge. The dislocation density in a metal increases with deformation or cold work because of dislocation multiplication or the formation of new dislocations. The more dislocations within a material, the more they interact and become pinned or tangled. This will result in a decrease in the mobility of the dislocations and a strengthening of the material. This process is known as cold working because the plastic deformation must occur at a temperature low enough that atoms cannot rearrange themselves. It is a process of making a metal harder and stronger through plastic deformation. Cold forming techniques are usually classified into four major groups:
- Squeezing
- Bending
- Drawing
- Shearing
Thermal Processing of Metals
Metals can be heat treated to alter the properties of strength, ductility, toughness, hardness, or resistance to corrosion. Many phenomena occur in metals and alloys at elevated temperatures. For example, recrystallization and the decomposition of austenite. These are effective in altering the mechanical characteristics when appropriate heat treatments or thermal processes are used. The use of heat treatments on commercial alloys is an exceedingly common practice. Common heat treatment processes include annealing, precipitation hardening, quenching, and tempering.
- Annealing. The term annealing refers to a heat treatment in which a material is exposed to an elevated temperature for an extended period and then slowly cooled. In this process, metal gets rid of stresses and makes the grain structure large and soft-edged so that when the metal is hit or stressed, it dents or perhaps bends rather than breaking; it is also easier to sand, and grind, or cut, anneal the metal.
- Quenching. Quenching refers to a heat treatment in which a material is rapidly cooled in water, oil, or air to obtain certain material properties, especially hardness. In metallurgy, quenching is commonly used to harden steel by introducing martensite. There is a balance between hardness and toughness in any steel; the harder the steel, the less tough or impact-resistant it is, and the more impact-resistant it is, the less hard it is.
- Tempering. The term tempering refers to a heat treatment used to increase the toughness of iron-based alloys. Tempering is usually performed after hardening to reduce some of the excess hardness. It is done by heating the metal to some temperature below the critical point for a certain period, then allowing it to cool in still air. Tempering makes the metal less hard while making it better able to sustain impacts without breaking. Tempering will cause the dissolved alloying elements to precipitate, or in the case of quenched steels, improve impact strength and ductile properties.
- Aging. Age hardening, also called precipitation hardening or particle hardening is a heat treatment technique based on the formation of extremely small, uniformly dispersed particles of a second phase within the original phase matrix to enhance The strength and hardness of some metal alloys. Precipitation hardening increases the yield strength of malleable materials, including most structural alloys of aluminium, magnesium, nickel, titanium, some steel, and stainless steel. In superalloys, it is known to cause yield strength anomaly providing excellent high-temperature strength.
Joining Processes
- Welding. In welding, one of the most common joining processes, two or more metal parts are joined to form a single piece by using high heat to melt the parts and allow them to cool, causing fusion.
- Brazing. Brazing is a metal-joining process in which a filler metal is melted and drawn into a capillary formed by the assembly of two or more work pieces. The filler metal has a lower melting point than the adjoining metal. Brazing differs from welding in that it does not involve melting the work pieces and soldering in higher temperatures for a similar process while requiring much more closely fitted parts than when soldering.
- Soldering. A technique for joining metals using a filler metal alloy with a melting temperature of less than 425°C (800°F). Because of this lower temperature and different alloys used as fillers, the metallurgical reaction between filler and workpiece is minimal, resulting in a weaker joint. In electronics assembly, the eutectic alloy with 63% tin and 37% lead (or 60/40, which is almost identical in melting point) has been the alloy of choice.
- Riveting. Riveting is one of the most ancient metalwork joining processes. A rivet is essentially a two-headed and unthreaded bolt that holds two other pieces of metal together. Currently, riveting still retains important uses in industry and construction. Solid rivets are used in applications where reliability and safety count. A typical application for solid rivets can be found within the structural parts of aircraft. Hundreds of thousands of solid rivets are used to assemble the frame of a modern aircraft.
Miscellaneous Metal Processing
- Sintering. Metal sintering is the process of compacting and forming a powdered metal by heat or pressure without melting it to the point of liquefaction.
- Laser Cladding. In the process of laser cladding, the metallic powder is blown through a movable laser beam (e.g., mounted on an NC 5-axis machine). The resulting melted metal reaches a substrate to form a melt pool. Moving the laser head makes it possible to stack the tracks and build up a three-dimensional piece.
- 3D printing. Metal 3D printing is based on sintering or melting amorphous powder metal in a 3D space to make any object shape. At a high level, the 3D printing process includes slicing a CAD file into discrete layers and then building that part layer by layer.